Onshoring of key supply chains is becoming increasingly important for the energy transition. To this end, the battery manufacturing supply chain outside of China is growing exponentially, but a major issue looms over the battery manufacturing process: waste.
The production of one gigawatt-hour of batteries generates about 5,000 metric tons of a chemical byproduct called sodium sulfate. While Chinese battery companies can sell this byproduct into the Chinese detergent market, manufacturers based in the US and Europe are struggling to find offtakers for this material and instead must pay for its disposal. In the competitive battery industry, the difference between sodium sulfate being a sellable product and a cost center for disposal is one of the main reasons why battery producers in the US and Europe can’t compete on cost with Chinese battery companies.
In extreme examples, sodium sulfate waste can even lead to battery projects being delayed or cancelled. Recently, a BASF-owned battery cathode plant in Finland was denied an environmental permit to operate owing to the large quantities of sodium sulfate waste the plant would generate.
Demand for batteries, primarily driven by electric vehicles, is projected to grow at a 22% CAGR through 2030, with the global battery manufacturing supply chain projected to be a $400B market by 2030. Meeting net-zero targets will require battery manufacturing to increase ~5x by 2030. Project delays and cancellations exacerbate the supply-demand gap – a discrepancy we cannot afford if we aim to decarbonize major industries and achieve global climate goals by 2050.
Put simply, sodium sulfate waste poses a colossal challenge for the battery supply chain and, resultingly, for progress towards our net-zero goals.
How Much Waste Should We Expect? What’s Being Done with It?
For every one ton of lithium ion battery material, 0.8 tons of sodium sulfate is generated as a byproduct. Battery manufacturing capacity outside of China is projected to grow ~6x between 2022 and 2030 to >2 terawatt-hours, leading to the production of >6 million tons per year of sodium sulfate waste.
What do you do with large quantities of sodium sulfate waste? This material, discharged as brine, must be disposed of, treated, or sold, but its uses are limited. We spoke to top battery cathode manufacturers, electric vehicle OEMs (original equipment manufacturers), and battery recyclers, all of whom stressed the need for a solution to address sodium sulfate byproduct. Aepnus Technology has taken on this challenge.
An Innovative Electrolyzer for Chemical Manufacturing
Aepnus Technology has a groundbreaking solution to the sodium sulfate waste problem. Aepnus creates value from sodium sulfate waste by converting it into valuable chemicals with its novel electrolyzer technology, the highest-performance and lowest-cost electrolyzer available.
Traditional electrolyzers, like alkaline and PEM, generate hydrogen and oxygen from water and require costly catalysts and high electricity consumption to split water’s chemical bonds.
Aepnus’ electrolyzer uses novel electrodes designed to split metal salts to produce chemicals. Aepnus’ process has two key advantages. First, it can replace expensive catalyst materials like iridium with less expensive materials, leading to 60% lower stack costs than PEM electrolyzers. Second, the electrolyzer is 30% more energy efficient than conventional electrolyzers, resulting in lower operating expenses.
With its superior opex and capex, Aepnus’ technology unlocks a new paradigm for producing chemical feedstocks that would otherwise not be economically viable.
Aepnus’ beachhead market is converting sodium sulfate into acids and bases, namely sulfuric acid and sodium hydroxide (also known as caustic soda). Sulfuric acid and sodium hydroxide are used extensively in battery manufacturing and recycling, and purchasing these reagents represents up to 30% of the opex for battery production or recycling plants.
By contrast, Aepnus can regenerate these chemicals from sodium sulfate, making $700 worth of sodium hydroxide and sulfuric acid per ton of sodium sulfate at a cost of only $350 (Figure 1). Using Aepnus’ solution reduces plant opex by up to 15% for customers while making the process more sustainable and mitigating a critical waste problem.
The electrolyzer’s performance and design deliver strong technoeconomic benefits, so Aepnus’ process and electrolyzer are an obvious choice for customers.
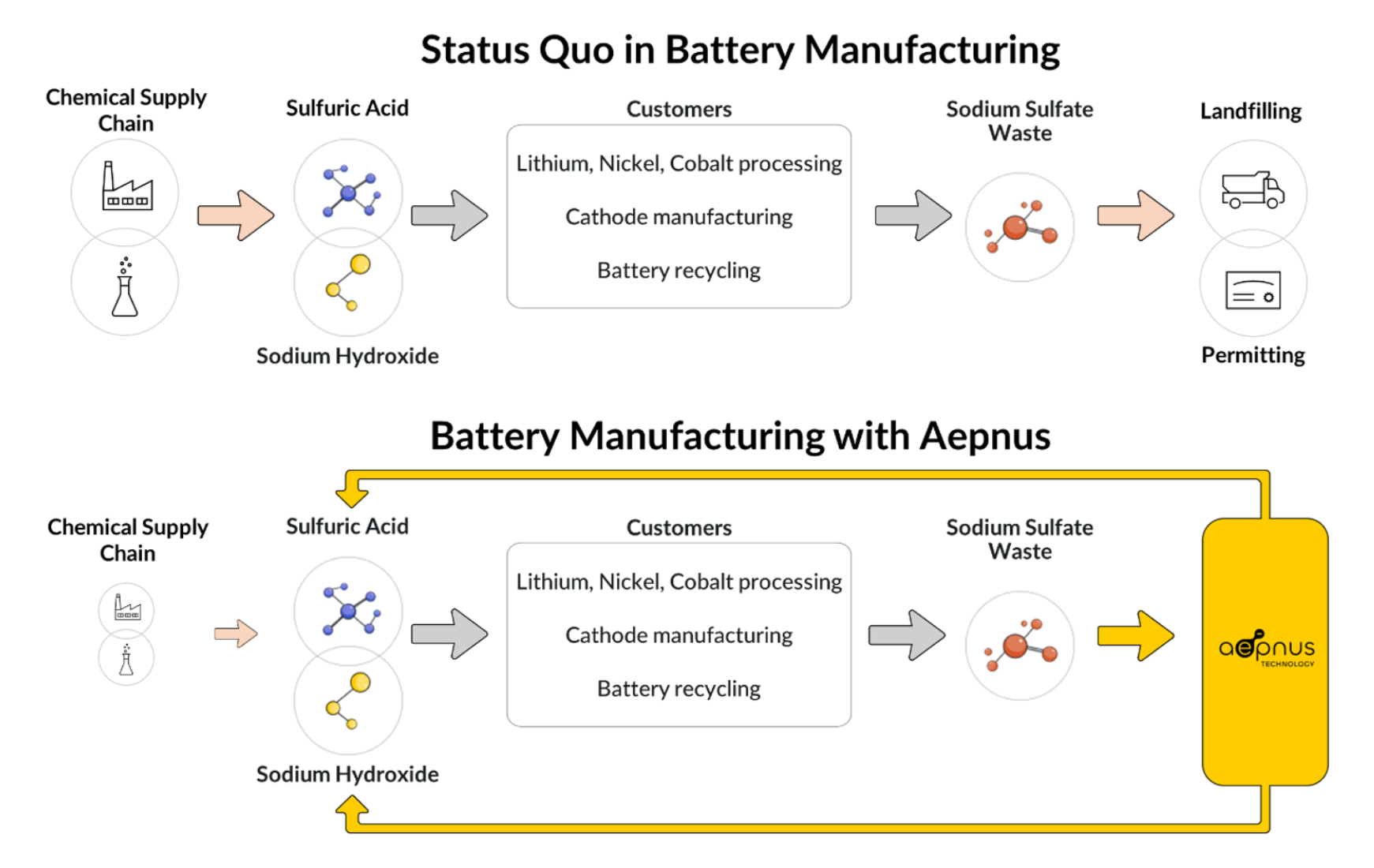
Electrochemistry to Displace Fossil Fuel-Powered Production
Electrochemistry is emerging as a promising pathway to electrify and decarbonize industrial processes that otherwise rely on fossil fuels to power them.
This thesis is supported by the history of the chloralkali process, in use since the late 1800s. The chloralkali process is the electrolysis of sodium chloride (table salt) into chlorine and sodium hydroxide. Chloralkali is used globally at a scale of ~60 million tons per year of sodium hydroxide and chlorine and is the primary production method for both.
The chloralkali industry proves that electrochemistry can be used to manufacture commodity chemicals at industrial scale. Aepnus is poised to leverage learnings from this industry as Aepnus grows.
The need for sodium sulfate processing pulled Aepnus into the battery manufacturing market as a beachhead. However, Aepnus’ electrolyzer technology has broader applicability for chemical processing and manufacturing in many other sectors that are currently powered by fossil fuels.
Lithium mining generates lithium sulfate, while battery manufacturers require lithium hydroxide. This conversion is chemically similar to that of sodium sulfate conversion. Consequently, Aepnus’ electrolyzer technology is perfectly suited to integrate into the lithium refining process, addressing another critical need in the battery supply chain.
Looking further, the Aepnus electrolyzer could have applications in metals refining like iron, zinc, nickel, and copper; low carbon cement; and even CO2 electrolysis to chemicals like carbon monoxide or ethylene.
The applicability of Aepnus’ electrolyzer to a broad array of chemicals combined with needs in the battery industry allows Aepnus to have multi-GT-scale impact on greenhouse gas emissions over the coming decades. In fact, we know that our own portfolio companies would use Aepnus electrolyzer in other markets when it becomes commercially available.
A Standout Team
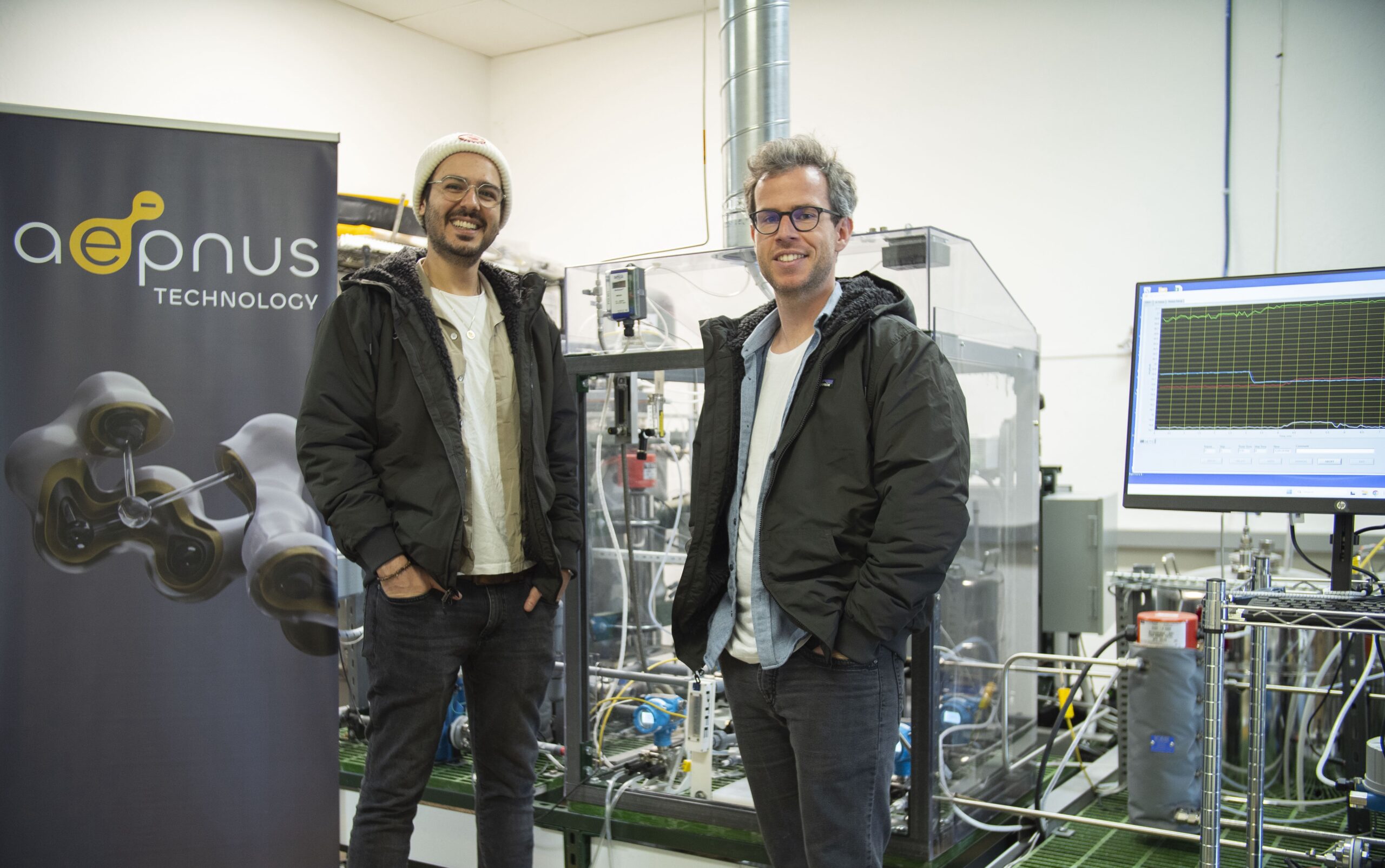
Aepnus’ technology was invented by two experienced researchers: Dr. Lukas Hackl, CEO, and Dr. Bilen Akuzum, CTO. The pair developed electrochemical systems for water desalination, water treatment, and large-scale energy storage while at Lawrence Berkeley National Laboratory, UC Berkeley, and Drexel University.
Dr. Hackl and Dr. Akuzum combine impressive expertise in electrochemistry with their unique aptitude for connecting with customers and devising innovative solutions to real-world problems. Their exceptional relationship-building skills have taken them around the world to engage with potential customers in industries such as battery manufacturing, battery recycling, mining, textiles, pigments, and cement production. This commercial drive is what allowed Dr. Hackl and Dr. Akuzum to uncover the massive problem and opportunity for innovation in recycling sodium sulfate waste.
Aepnus’ novel electrochemical technology not only fulfills an urgent need in the battery industry, but it also supports the essential shift towards electrification of chemical production more broadly. With an exceptional leadership team and expansive market applications, Aepnus is well-positioned to grow and scale quickly. This investment strongly aligns with our commitment to advance innovative solutions that can decarbonize major industries and drive significant progress towards our collective climate goals.
Visit Aepnus’ website to learn more or contact Micha Ben-Naim for an intro to the team.